Sustainability
Sustainability Report
Long-term value creation at the CPH Group is predicated on ensuring that its business activities are sustainable in economic, social and environmental terms. Recycling is deeply embedded in the Group’s DNA.
Sustainability anchored in corporate strategy
Sustainable value creation has been instrumental to the business success of the CPH Group over the past 200 years. The approach is firmly anchored in the Group’s corporate strategy. CPH pays due and full regard to the needs of its business partners, its employees and the natural environment by assuming full and constant responsibility for all its business conduct in economic, social and ecological terms.
Economic sustainability is the foundation of the Group’s industrial activities, where continued long-term development has always been centrestage. CPH creates added value for its customers by providing high-quality products and services. Its employees ensure that the Group remains strongly innovative and effectively competitive in its target markets. Their safety, health and continued training are all top priorities. Avoiding and reducing emissions, waste water and other waste has been integrated into the planning of all three business divisions for many years now. And responsibility for ecological and quality issues is assigned to specially trained employees who report directly to top management.
Recycling is in the Group’s DNA
The Paper Division, the biggest of the Group’s three divisions, is a recycling business that helps greatly to ensure the careful use of valuable wood resources by recovering wood-containing waste paper and turning it into new printing and publication paper products. The division took over the waste paper recovery and reprocessing activities of Papierfabrik Utzenstorf AG at the beginning of 2018, and is now Switzerland’s biggest waste paper recycler. APS Altpapier Service Schweiz AG, the new subsidiary founded for these purposes, channels several hundred thousand tonnes of waste paper that is recovered in Switzerland each year into these new uses. In doing so, it ensures that the CPH Group makes a major contribution to avoiding high transport costs and reducing carbon dioxide emissions. The Group has been setting its own goals for cutting its carbon emissions that go beyond those required by law for many years now. And thanks to various actions, such as replacing coal power with natural gas in China and procuring the steam needed in its Perlen paper production from the nearby Renergia waste incineration facility, the CPH Group has reduced the annual CO2 emissions at its eight production sites worldwide from 80 850 tonnes to 16 493 tonnes over the past five years.
The CPH Group also takes its responsibility towards its employees very seriously. The first company health insurance scheme was established for workers at its Uetikon site as early as the 1860s. And 2018 marked the centenary of the foundation of the Group’s occupational pension scheme for Swiss-based personnel. With the closure of its Uetikon site, too, the Group strove to find optimum solutions in social and economic terms for the 85 staff affected. Almost all these personnel had been found a suitable alternative by the time the site was handed over to its new owner Canton Zurich in summer 2018.
The CPH Group is further living up to its responsibilities in terms of the clean-up required of the Uetikon site following its many years of industrial use. The Group is meeting 80% of the costs of cleaning up the lake floor adjacent to the site. The corresponding provisions for this were made back in the 2016 financial year.
Economic sustainability
The CPH Group has diversified its industrial activities into different business segments. This is intended to better cushion the Group against fluctuations in its sales markets, some of which are volatile and cyclical by nature. The Group strives to create long-term value for its stakeholders by offering products that are tailored to its markets and their needs, along with interesting work opportunities and attractive shareholder returns. The Group has set itself the following medium-term financial targets:
- organic net sales growth of more than 3% a year
- an EBITDA margin of over 10%
- an equity ratio above 50%
- liquidity of at least CHF 30−50 million
- annual operating investments of CHF 15−20 million.
Social sustainability
The CPH Group makes every effort to secure the best employees and to promote, support and further train them as effectively as possible in their working world. An open communications culture, a management and leadership that put CPH’s values into practice and a safe, healthy and varied work environment are all intended to encourage and further its employees commitment to their work and their identification with the Group, their company and their individual role. The CPH Group also attaches great importance to ensuring a sound work/life balance. At its German site, for instance, the Group offers part-time working models to make the transition to retirement a smoother and more flexible experience.
Three quarters of the workforce participated in a survey in autumn 2016 on the issues of workplace, professional development, leadership, communications, innovation, customers, strategy and involvement. A number of actions were adopted in the light of the results, the benefits of which should be seen in the next such survey, which is planned for 2019. The survey is conducted every three years on a groupwide scale. Staff turnover amounted to 8.3% in 2018, which was below the 8.8% of the previous year. CPH numbers many long-serving employees: some 21% of the 2018 workforce had been with the Group for 20 years or more. Service anniversaries are duly marked with awards ranging from small gifts to parties, depending on local customs. Many former employees also remain close to CPH, and meet up annually at retiree events which are organized by the Group.
Year-end total personnel numbers rose from 1 019 to 1 081. The increase was due largely to the expansion of the Packaging workforce, which passed the 400 mark for the first time. The majority of the Group’s employees − 66% − are involved in production. Around half the total workforce are based in Switzerland. The CPH workforce is also highly diverse, employing individuals of 32 nationalities. Women made up 17.3% of the total 2018 workforce. The Group’s US operations offer special communications training courses for female employees; and training is also regularly conducted on the issues of harassment and diversity.
Salary policy
CPH pursues a fair and reasonable groupwide salary policy that is closely aligned to local customs and conditions. This policy is intended to offer salaries that pay due regard to the demands of the position, the conduct and performance of its occupant and general market levels. It also rewards above-average performance, via bonus payments or (with management positions) via a variable salary component that is linked to the achievement of individually set performance goals and to divisional results. The Group made individual salary adjustments in 2018. The total cost of salaries, occupational pension scheme payments and basic and further training amounted to CHF 92.4 million. All employees at the Perlen and Utzenstorf sites are subject to a collective labour agreement (CLA). Employees at the Müllheim site in Germany are subject to the CLA of the Industriegewerkschaft Bergbau Chemie Energie (IGBCE). Elsewhere, personnel worked under individual employment contracts.
Initial and further training
Switzerland and Germany maintain a “dual” education system that combines company apprentice placements with attendance at vocational schools. The system is a key element in both countries’ economies and business sectors, providing the skilled professionals needed to maintain their competitive credentials in the longer term. Through its own vocational training activities at its Swiss and German sites the CPH Group not only lives up to its social responsibility: the employees it trains play their full part, too, in achieving its business goals.
A total of 37 apprentices and interns were on the CPH Group payroll at the end of 2018. Thirteen apprentices completed their courses during the year, eight of whom could be given permanent positions. The Group’s apprentices meet each year at the Apprentices Day, a group-level further training event. Two young asylum seekers were also integrated into the work process at the Perlen site. After completing an internship, they embarked (or are about to embark) on training as plant operators. Two members of the Group’s German workforce are currently completing a dual-education course in business administration at the Baden-Württemberg Cooperative State University under which the students spent alternating three-month periods at the university and at the company. Every CPH Group employee spent an average of 2.5 days on in-house or external training in 2018. The employees at the Group’s Donghai (China) site, for instance, were thoroughly prepared for the coming switch to a three-shift operation. The Group spent a total of CHF 1.2 million on initial and further training for its employees in the course of the year.
Continuous improvement
Winning new customers and securing their long-term custom are among the core aspirations of the CPH Group’s sales and distribution strategy. The Group’s divisions maintain a constant dialogue with their customers to systematically monitor their satisfaction and identify possible improvements. The divisions also conduct customer satisfaction surveys every two to three years which address such areas as service quality, technical support, product quality, product range, delivery times, reliability, complaints management and pricing. The Group’s Continuous Improvement Process (CIP) is a further key element in its ongoing endeavours to ensure its future development and further raise quality and efficiency, and CIP training is conducted every year in all three divisions. The 582 CIP ideas and 99 group CIP moderations of 2018 produced a number of proposals to help enhance efficiency, improve safety and ease environmental impact. All in all, these proposals delivered an annual benefit of some CHF 1.0 million. The proposals included:
- In Chemistry: feeding the raw materials that fall out of the drums during molecular sieve manufacture back into the production process not by collecting them manually in barrels but by channelling them via a chute into a self-emptying container. Savings potential: around CHF 66 000 a year.
- In Paper: requantifying the amounts of starch used to fix the coating in the manufacture of coated paper products while still retaining the previous finish quality. Cost savings: around CHF 100 000 a year.
- In Packaging: creating a clean room for the finishing process, thereby increasing air exchange rates and lowering particle volumes, which has halved the number of times the rolling machines need to be cleaned and thus extended their running times. Annual savings: around CHF 46 000.
Occupational safety
CPH conducts regular training to help identify dangers and prevent accidents at all its operating sites. Any incidents or accidents that do CO2 emissions (tonnes) occur are systematically analyzed to help prevent their recurrence. The 3.3 occupational accidents per one hundred employees in 2018 (which compares to 2.1 for the previous year) remained low for a manufacturing concern. The year saw one fire in a paper store, which caused limited damage and no personal injuries. One outside individual was seriously injured, however, in an accident that occurred during maintenance work. The occupational accident-related absence rate for 2018 amounted to 0.2%, unchanged from the previous year.
Healthcare
The Group’s various operations offer numerous healthcare facilities, such as free flu vaccinations and annual health check-ups. Many of them also contribute to employees’ fitness centre subscriptions. The site in Germany further teamed up with a number of other companies to conduct a health and safety afternoon to sensitize personnel to such issues. The sickness-related absence rate for the year was low again at 2.0%, unchanged from 2017.
Social involvement
Numerous employees of the CPH Group are involved in activities for the communal good both in and outside their companies. Some serve as company paramedics or company fire officers, while others take part in charity projects in their leisure time. Employees in the USA, for instance, participated in a charity run in the course of the year. Other group operations supported communal projects at the local level, such as in the integration of asylum seekers as mentioned above.
Ecological sustainability
The CPH Group’s environmental reporting year runs from the beginning of November to the end of October.
Use of resources
In tonnage terms, the largest proportion of resources used within the CPH Group is in the Paper Division, which has recovered paper as its key raw material. Perlen Papier recycled 468 137 tonnes of recovered paper in its operations in 2018, slightly more than the 463 990 tonnes of the previous year. Some 82% of this recovered paper was collected in Switzerland, with the rest coming from abroad. Around 10% of the paper was delivered to Perlen by rail (compared with 15% in the prior-year period). Perlen Papier also turned 109 263 bone-dry tonnes of round wood and woodchip into wood fibre in 2018 (2017: 109 579 bone-dry tonnes). CPH strives to minimize the transport distances involved: all of the round wood and 80% of the woodchip used come from Swiss sources. This latter figure should be further raised if possible. Perlen Papier is also a member of ECO SWISS, Swiss business and industry’s environmental protection organization, and of further bodies promoting sustainable forestry.
Perlen Packaging’s film manufacturing process uses unplasticized PVC, which is composed of 43% ethylene and 57% sodium chloride. Compared with other oil-based polymers, PVC boasts a better product carbon footprint for its overall life cycle. Wherever possible, waste and scrap material from the various manufacturing steps are fed back into the production process as secondary raw materials. The raw material utilization rate for 2018 was 97% for PVC (compared to 98% in 2017) and 99% for PVdC (compared to 98% the previous year). Perlen Packaging is also actively involved in the VINYLPlus programme, which promotes PVC recycling.
Energy
Over 90% of the energy used by the CPH Group in 2018 was for its paper production. Electricity is the Group’s main energy source, and its consumption increased groupwide from 2 426 to 2 648 terajoules (TJ). The second most important energy provider was steam at 1 116 TJ (2017: 1 078 TJ). This was procured for paper production in Perlen from the nearby Renergia waste incinerator facility. Group gas consumption declined slightly from 355 to 344 TJ. For environmental reasons, the use of coal as an energy source in Donghai was reduced from 22 TJ to zero, with natural gas and pellets serving as the replacement energy sources. The CPH Group’s overall energy consumption for 2018 totalled 4 904 TJ, up 276 TJ or 5.6% from its prior-year level.
Emissions, waste water and solid waste
The CPH Group sets its own goals to reduce its emissions which are more rigorous than those required by law. As a result, its Perlen facility was exempt in 2018 from any carbon dioxide (CO2) levy. The Perlen plant emits around 10% of the maximum CO2 legally permitted. Total CO2 emissions from CPH’s sites amounted to 16 493 tonnes, down from the 16 554 tonnes of 2017. Of these, 9 435 tonnes derived from paper production and 5 441 tonnes from the Chemistry Division. The operation in Germany has been consistently using green electricity since 2018 in line with ISO 14001 environmental management standards. The sales of carbon credits generated an income of CHF 0.9 million.
Exhaust air cleaning systems are installed at the Group’s production facilities. Emergency concepts have been devised to cope with any production malfunction. These centre primarily on the scenario of fire. The Perlen site has its own fire service, which can be deployed if needed. The waste water produced by the Group’s Perlen, Louisville and Donghai plants is processed in their own treatment facilities. An expansion of these is planned at the Donghai plant, in view of the sizeable recent increases in the plant’s production volumes. Total groupwide waste water volume for the year amounted to 6.67 million cubic metres, a decline from the 7.46 million cubic metres of 2017. The solid waste produced by the Group’s production activities primarily consists of sludge and ash, which, thanks to excellent dewatering processes, can be re-used in brickworks and in the cement industry. The solid waste generated in the production of molecular sieves consists of silicate-aluminium-clay compounds, and is of natural origin. As a result, it can be freely reburied. With the solid waste produced in paper and film production, the biomass is used to produce heat and electricity in the Group’s own Perlen facility.
Brand policy
The CPH Group pursues a clear brand policy. At the company level the Group maintains five brands, which are aimed at differing markets and target groups. CPH Chemie + Papier Holding AG (“CPH”), the Group’s holding company, is not operationally active, but serves as the industrial conglomerate’s umbrella brand towards its stakeholders.
The Group’s three divisions operate under their corporate brands of “Zeochem”, “Perlen Papier” and “Perlen Packaging”. These were supplemented in 2018 with the addition of “APS Altpapier Schweiz” as a further corporate brand of the Paper Division. APS Altpapier Schweiz was adopted as a separate brand because the company operates independently in the waste paper procurement segment.
The corporate brands enjoy outstanding acceptance and high familiarity in their target markets. They are bywords for both tradition and innovation. Perlen Papier has been operating since 1873. Perlen Packaging originally emerged from the Paper Division at the same Perlen location, and has only been trading under its own Perlen Packaging brand for some ten years now. The Zeochem brand has been used since 1979, and originated at the Chemistry Division’s US operation. To further sharpen the profiles of the Group’s corporate brands in their various markets, the names of all the subsidiaries in the Chemistry and Packaging Divisions were standardized in 2018 to Zeochem and Perlen Packaging respectively.
The Group’s various constituent companies maintain a product brand architecture that uses the same standard prefix to identify and assign products within each division. Thus, all Zeochem products begin with Zeo- (such as Zeoprep), all Perlen Papier products begin with Perlen- (such as Perlentop) and all Perlen Packaging products begin with Perla- (such as Perlalux). These product names are also registered as trademarks wherever possible, to protect them from counterfeiting activities.
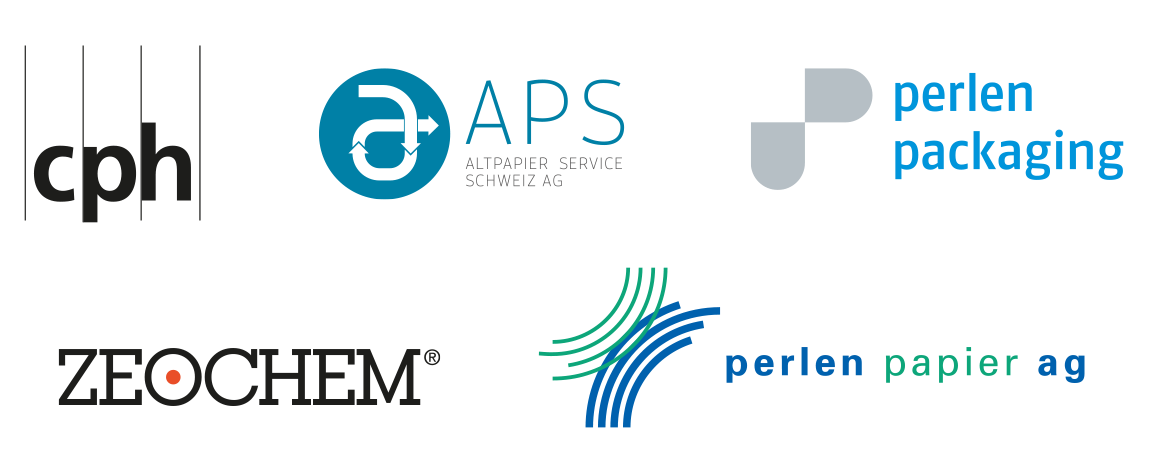
Quality
Consistently high quality is a hallmark of all the products of the CPH Group. This makes stringent demands on its processes, which are audited to international standards (see table below). Production sites are subjected to regular audits by customers and by independent certification bodies.
The Packaging Division aligns its film manufacturing to the pharmaceuticals sector’s Good Manufacturing Practice (GMP) standards. The CPH Group also promotes energy efficiency in the climate protection project of the Swiss private sector’s energy agency, and is a member of Responsible Care, a global continuous improvement initiative in the environmental, health and safety fields.