Continous improvement
Innovation born of motivation
Constantly improving product, process and service quality to create and supply high-quality products and thereby maintain a strong competitive position in its target markets is a core competence of the CPH Group.
Innovation, within the CPH Group, means developing new products and services to meet customers’ needs and ensuring that replicable industrial-scale high-level quality is consistently maintained. In doing so the Group can draw on decades of experience in mastering and optimizing complex industrial processes, and abides by ISO and GMP quality standards in all its work activities. The Paper Division, to take one example, was able to maintain its viability between 2010 and 2020 – a period which saw product prices halved on the paper market – by raising its productivity, enhancing its processes and reducing its fixed and input costs.
For more than 20 years now, a Continuous Improvement Process (CIP) has been successfully serving as a key innovation and quality management tool within all three of the Group’s divisions. The CIP is based on the principle of Kaizen, from the Japanese kai (‘change’) and zen (‘for the better’).
The CIP enables process enhancements and cost savings to be identified and achieved which improve the quality of products and services and raise satisfaction among both customers and employees. Every contribution is valued which helps to optimize processes, save energy, ease pressures on the environment or resources, enhance safety and improve the working atmosphere.
It is CPH’s employees who are the bedrock of its CIP, submitting hundreds of improvement ideas every year either individually or in teams. All such submissions are evaluated under a clearly structured procedure. And experience shows that around half of them will result in concrete practical actions.
In 2022 the Paper Division established a new database accessible to all employees in which all CIP suggestions are systematically processed.
Three reactors connected – production doubled
Three reactors are used in the manufacture of Methanol D4 at the Chemistry Division’s Rüti site. One of these automatically mixes the reaction gas; with the others, the gas must be manually mixed before every production batch.

Dzemilj Abdiji releases the Methanol D4 at the end of each reaction. And he had the idea of connecting the three reactors. So the automated reactor now provides all three facilities with the gas mix required. The result: doubled production volumes and more consistent quality, too.
Double-rolling makes better use of container capacity
Some of the coated PVC films which are manufactured in Suzhou, China are transported to Perlen on pallets, as what are known as mother reels. But since only a limited number of pallets will fit into a transport container, and such reels cannot be stacked, less than optimal use can be made of the container’s volume capacity.
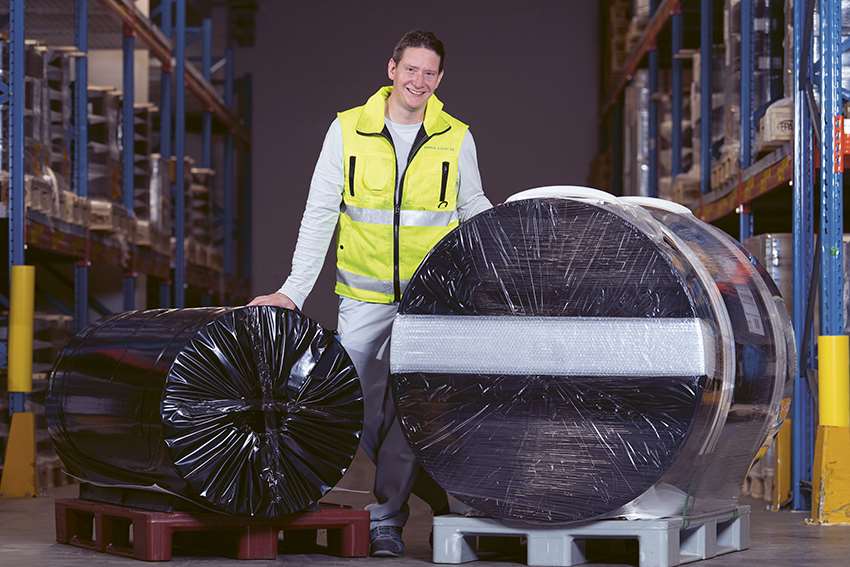
Philipp Gamma had the idea of doubling the length of the film on each mother reel. The new approach takes up less storage space and makes better use of transport container capacity. And it has reduced the associated transport costs by 15 to 20 per cent.
Additional sorter cuts energy consumption by 30%
The wood pulp produced from waste wood in Perlen Papier’s thermomechanical facility is subsequently separated in two main sorters from the wood fibres that cannot be immediately used as they need to be further ground. But these two main sorters were repeatedly operating at their capacity limits.
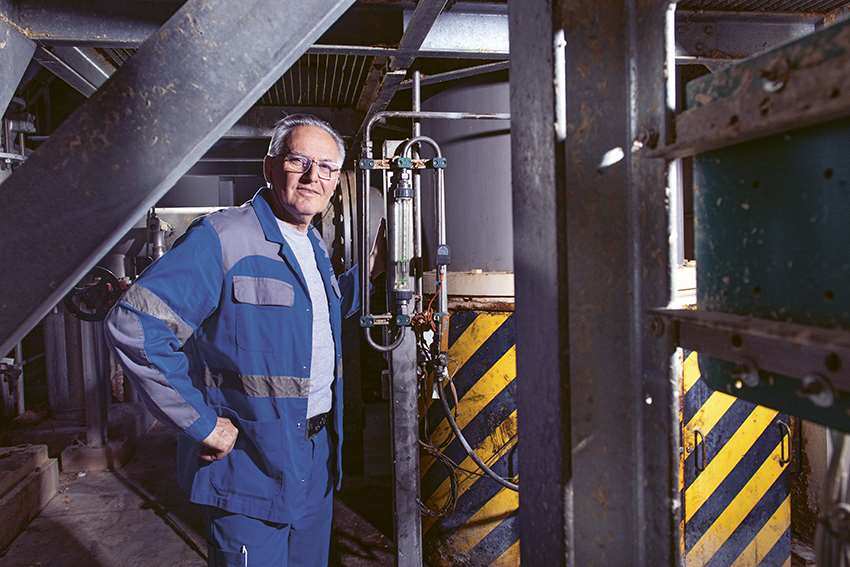
Sopi Gezim hit upon the idea of converting an existing secondary sorter into a further main sorter. With three main sorters, higher pulp volumes can now be processed at lower running levels. This has reduced the energy required per tonne of sorted pulp by 30%. The innovation has not only lowered costs: it benefits the environment, and has raised pulp quality, too.