Success stories Chemistry
A new centre of innovation
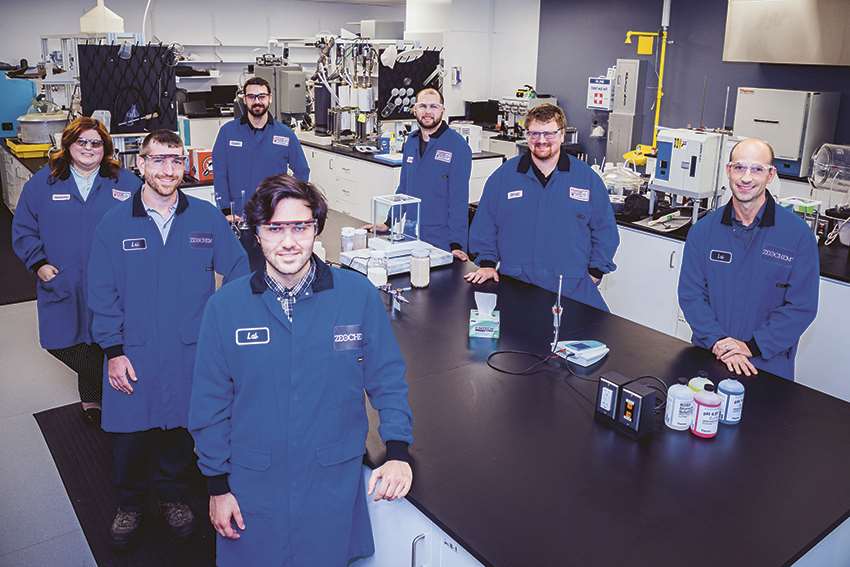
The R&D team in their new Louisville laboratory
The new service building at the US site provides an innovation centre for molecular sieves and numerous further workplaces, all in a highly collaborative environment.
The Chemistry Division’s Louisville (USA) operation moved into a new building in summer 2022 that brings all its production, R&D, quality management and sales staff and all its management personnel under one roof. The result: shorter communications channels and a collaborative working environment which features both teamwork and quiet areas for the employees concerned.
The new Molecular Sieve Innovation Center is home to seven employees working to enhance existing products and develop new ones for a wide range of applications from drying natural gas and ethanol to removing impurities from gases and liquids and concentrating ambient oxygen. The Louisville R&D team brings around half a dozen new and modified products to market maturity every year, including customer-specific applications that are developed to meet particular performance demands.
Creative and motivated employees with strong technical expertise and an innovative working environment are vital to maintaining and further sharpening the division’s competitive edge. Products newly launched within the previous five years accounted for 10.3% of the Chemistry Division’s total net sales in 2022.
Investing in new production facilities
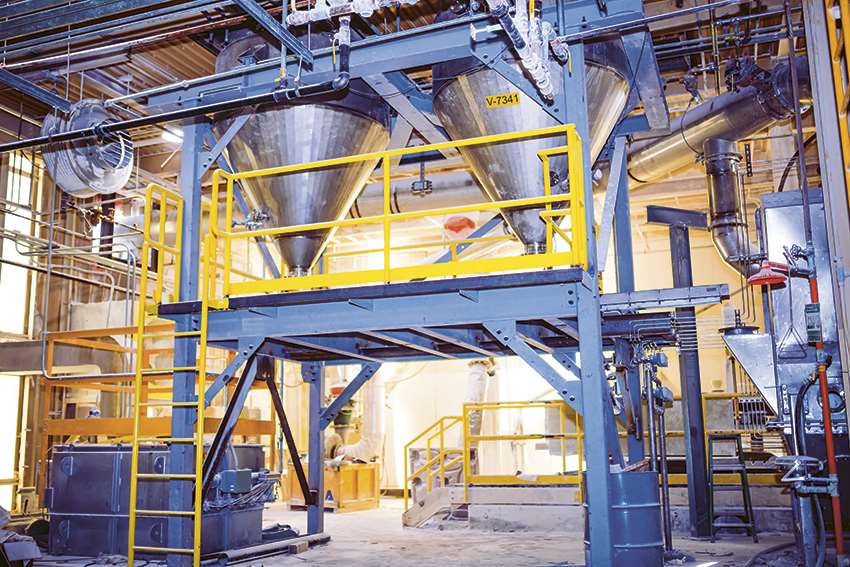
The Louisville production plant for lithium molecular sieves
The demand for molecular sieves for concentrating medical and industrial oxygen has risen steeply over the past few years. These complex high-performance lithium-based products are used in medicine to treat respiratory disorders. 2022 saw the entry into service of a new production facility at the Chemistry Division’s US site which has raised the manufacturing capacities for such lithium-based products by around 40%.
The capacities for manufacturing molecular sieves for use in purifying ethanol and concentrating industrial oxygen were also raised by 40% at the division’s Donghai site in China, by automating a previously manual production line.
Windows are a further rapidly growing application for the Chemistry Division’s products. A new technology has been gradually gaining ground over the past few years which is designed to prevent misting within multi-pane windows. In the past, the spacers between such panes were usually of hollow metal filled with molecular sieve beads. Today’s spacers, by contrast, are made of thermically optimized plastic into which the molecular sieve has already been incorporated in powder form. To meet the high demand for such molecular sieve powders, the division’s Zvornik operation in Bosnia and Herzegovina has put a new calcining plant into service which has doubled previous capacities.
Deuterated products help make medicines easier to take
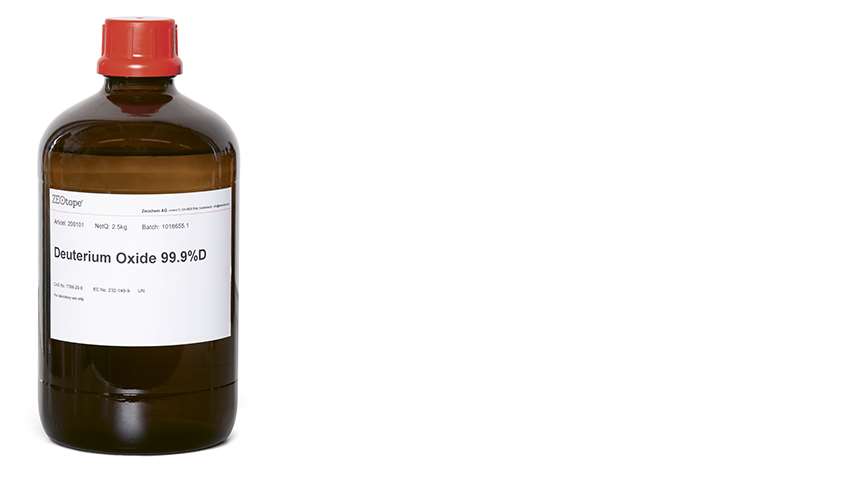
The Chemistry Division produces various deuterated molecules for research and development projects within the pharmaceutical industry and for production ventures. In view of the industry’s growing interest in such deuterated molecules, the division is now intensifying its focus on introducing new products in the field.
Adding deuterium to a carbon chemical compound helps to slow the release of an active agent – in a medicine, for example. This is due to the kinetic isotope effect, which strengthens the bonding between the deuterium and the carbon. The benefit to patients: lower dosages required and better tolerance of the medicine concerned.