Sustainability
“Recycling is in our DNA”
Sustainability is essential to long-term value creation at the CPH Group. The Group has vastly reduced its CO2 emissions over the past few years. Perlen Papier will also be Switzerland’s sole recycler of recovered paper from 2018.
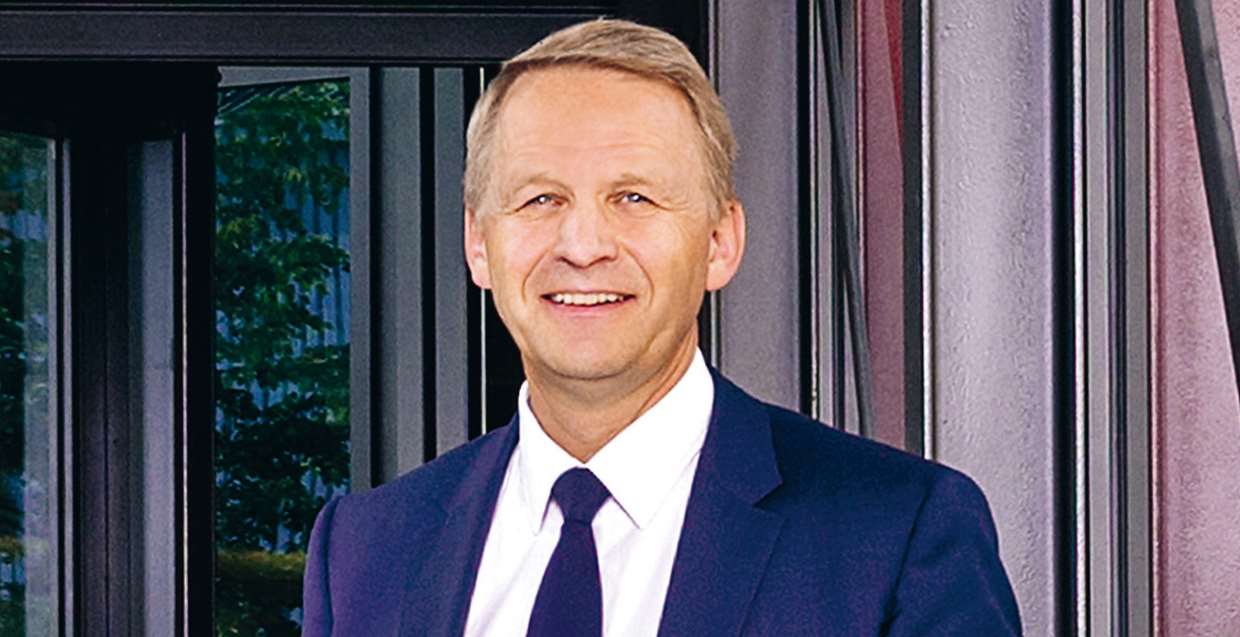
Peter Schildknecht, Group CEO
What importance do you attach to sustainability at the CPH Group?
Peter Schildknecht: We are active in business segments that can have quite an impact on the environment, and we’re fully committed to sustainable value creation. We make sure that, through our economic, social and ecological conduct, we meet the needs of our business partners, our employees and the natural world around us. Economic sustainability is the cornerstone of our 200 years of business activities. Here we put a particular focus on continuous long-term development. We create added value for our customers by manufacturing and offering high-quality products. Our employees are the heart within and the drive behind our Group. They are the ones who ensure our innovative strength. And their basic and further training, their security and their health are all top priorities. We also take responsibility through our sparing use of resources. Avoiding and reducing emissions, waste water and solid waste have been integrated into the planning within each of our three divisions for several years now. And we have specially-trained personnel responsible for environmental and quality affairs who report directly to our Group Executive Management.
Sustainability efforts often entail higher costs. So is there a conflict of objectives here?
On the contrary: a lot of these endeavours actually mean lower costs. Every resource that we can save or re-use in our production is firstly good for the environment and secondly good for CPH. And our social commitment translates into motivated and satisfied employees. So we see it all as a win-win situation.
What kind of feedback do you get from your stakeholders on your sustainability endeavours?
The feedback from our stakeholders is very important to us. We conduct regular surveys of our customers and our employees, and we utilize the feedback we get from these to further enhance our products and our processes. We publish − at our customers’ request − the carbon footprint created by producing one tonne of paper; we offer FSC-certificated paper products; and we have our operating locations certified to environmental and occupational safety standards. As a rule, though, our customers aren’t yet willing to pay higher prices for products with higher sustainability credentials.
What sustainability successes have you already enjoyed?
We have voluntarily set ourselves goals to reduce our carbon dioxide emissions that go beyond the targets required by law. And we have taken a range of actions here that have lowered our annual CO2 emissions from 86 000 tonnes to 17 000 tonnes over the past five years. Also, our Paper Division is now the only recycler of recovered paper in Switzerland, so it’s playing a key role in the re-use of waste paper and thus the protection of the forests.
Recycling is in our DNA. The sale of our Uetikon operating site permits the construction of a new cantonal secondary school, which is an ideal solution for the coming generations and the local community. We are also assuming our responsibility here for the removal of any pollutants in the ground. And we have striven to minimize the social impact of the job losses that are unavoidable with the closure of this operation. In fact, alternative arrangements have been found for almost every one of the 85 employees affected.
What will you be focusing on in future in sustainability terms?
We will be intensifying our Continuous Improvement Process or CIP. Changes big and small should − and have to − come from our employees and be championed by them, too, if they are to have their full effect, to the benefit of all our stakeholders.
Sustainability Report
Social sustainability
Three-quarters of the group workforce took part in a survey in autumn 2016 which sought their views on the issues of workplace, professional development, leadership, communications, innovation, customers, strategy and commitment. This survey is conducted groupwide every three years. The latest poll showed improvements in the commitment and satisfaction categories, while leadership and appreciation in particular earned significantly higher marks. The areas of employee development and improvement management still have more potential. With the results clearly showing differing focus areas among the Group’s divisions and operating locations, 43 segments were created, and actions were defined for each of these with due employee involvement. These actions were then implemented by the end of 2017. One of them related to a redesign of the Continuous Improvement Process (see the CIP section below).
Annual group staff turnover amounted to 8.8% in 2017, down from the 9.7% of the previous year. The CPH Group workforce includes a sizeable number of long-serving employees: 42 of them celebrated 20th, 25th, 30th, 35th or 40th service anniversaries in the course of the year. Many former employees also remain close to the Group and meet once a year for a retirees’ event which is organized by CPH. Year-end employee numbers rose from 985 to 1 019, owing largely to the expansion of the Packaging Division’s workforce. The majority of the Group’s employees − 67% − are involved in production. The proportion of the total group workforce who are based in Switzerland declined from 61% to 55% (see charts).
Salary policy
CPH pursues a fair and reasonable groupwide salary policy that is closely aligned to local customs and conditions. This policy is intended to offer salaries that pay due regard to the demands of the position, the conduct and performance of its occupant and general market levels. It also rewards above-average performance via a variable salary component that is linked to the achievement of individually set performance goals and to divisional results. Once again, no across-the-board salary increases were awarded in 2017. The CPH Group spent CHF 84.5 million on salaries, company pension scheme contributions and staff training over the course of the year.
All employees at the Perlen site are subject to a collective labour agreement (CLA). Employees at the Müllheim site in Germany are subject to the CLA of the Industriegewerkschaft Bergbau Chemie Energie (IGBCE). The Uetikon silicate chemistry operation had its own staff association until the end of 2017. Elsewhere, personnel worked under individual employment contracts.
Initial and further training
CPH attaches great importance to the training of its own junior personnel. Its Swiss and German operations have active apprentice programmes offering basic professional training. Some 39 apprentices were on the group payroll at the end of 2017. The year also saw the first-ever training of two plant operators and a laboratory chemist in Germany. Fourteen apprentices completed their courses during the year. All the apprentices of the CPH Group also meet once a year for an Apprentices Day of further group-themed training. The Paper Division made its first appearance as an exhibitor at the ZEBI, Central Switzerland’s training fair, in 2017. The CPH Group invested a total of CHF 0.6 million in the basic and further training of its employees over the course of the year.
Continuous improvement
CPH’s Continuous Improvement Process (CIP) is a vital element in the Group’s constant endeavours to further develop and enhance product quality. A series of four workshops was held in the Paper Division in 2017 to remodel its CIP and ensure that it makes a major contribution once again to CPH’s success. While CIP is already well established in the Packaging Division, the Chemistry Division aims to further intensify its CIP activities in 2018. The 756 ideas submitted to the CIP in 2017 and the 53 group moderations held in the course of the year produced a number of proposals that have helped raise efficiency, enhance safety and protect the environment, and should add some CHF 1.2 million to annual earnings results.
Occupational safety
CPH conducts regular training to help identify dangers and prevent accidents at all its operating sites. Any incidents or accidents that do occur are systematically analyzed to help prevent their recurrence. The number of occupational accidents per one hundred employees for 2017 − 1.3 − remained low for an industrial manufacturing concern (and compares to 1.5 for the previous year). Fortunately, the year remained free of any major occupational accidents.
Healthcare
The Group’s various operations offer numerous healthcare facilities, such as free flu vaccinations and health check-ups. The sickness-related absence rate for the year was low again at 2.0% (compared to 2.5% for 2016).
Ecological sustainability
The CPH Group’s environmental reporting year runs from the beginning of November to the end of October.
Use of resources
In tonnage terms, the largest proportion of resources used within the CPH Group is recovered paper, the key raw material of the Paper Division. Perlen Papier recycled 463 990 tonnes of recovered paper in its operations in 2017, just below the 464 492 tonnes of the previous year. Over 50% of this recovered paper is collected in Switzerland, with the rest coming from abroad. Some 15% of the paper was delivered to Perlen by rail (compared with 16% in 2016). Perlen Papier also turned 109 579 bone-dry tonnes of round wood and woodchip into wood fibre in 2017 (2016: 109 000 bone-dry tonnes). CPH strives to minimize the transport distances involved: all of the round wood and 70% of the woodchip used come from Swiss sources. The latter figure should be raised to 80% by 2020. Perlen Papier is also a member of ECO SWISS, Swiss business and industry’s environmental protection organization, and of further bodies promoting sustainable forestry.
Perlen Packaging’s film manufacturing process uses unplasticized PVC, which, is composed of 43% ethylene and 57% sodium chloride. Compared with other oil-based polymers, PVC boasts a better product carbon footprint for its overall life cycle. Perlen Packaging used 29 299 tonnes of PVC and 3 210 tonnes of PVdC in 2017. Wherever possible, waste and scrap material from the various manufacturing steps are fed back into the production process as secondary raw materials. For 2017 the raw material utilization rate was raised from 96% to 98% for PVC and from 95% to 98% for PVdC. Perlen Packaging is also actively involved in the VINYLPlus programme, which promotes PVC recycling.
The most important raw materials in the Group’s silicate chemistry operations are sodium silicate, aluminium hydrate, sodium hydroxide, sulphuric acid and lithium chloride, of which 14 835 tonnes were used in 2017 (2016: 17 677 tonnes). The division terminated its own synthesis activities at its Uetikon site at the end of 2017, and will now obtain its raw materials here in filter cake form. Its fertilizer production consumed 11 793 tonnes of nitrogen, potassium and phosphorus compounds in 2017 until it ceased in summer (2016: 14 135 tonnes). Some 85% of this was delivered by rail.
Energy
Over 90% of the energy used by the CPH Group in 2017 was for paper production. Electricity is the Group’s main energy source, and its consumption declined groupwide from 2 430 to 2 426 terajoules (TJ). The second most important energy provider was steam at 1 078 TJ (2016: 1 018 TJ). This is procured for paper production in Perlen from the nearby Renergia waste incinerator facility. Group gas consumption declined slightly from 387 to 355 TJ. The use of coal as an energy source for the Lianyungang plant in China was reduced from 36 to 22 TJ for environmental reasons. The replacement of coal with other energy sources should be completed in 2018. The CPH Group’s overall energy consumption for the year amounted to 4 629 terajoules, virtually unchanged from the 4 621 terajoules of 2016.
Emissions, waste water and solid waste
The CPH Group sets its own goals to reduce carbon dioxide (CO2) emissions which are more rigorous than those required by law. As a result, its Perlen and Uetikon facilities were exempt in 2017 from any CO2 levy.
The conversion of the Perlen waste incinerator to a biomass facility also had a positive impact on the Group’s CO2 emissions from non-renewable resources. Total CO2 emissions from CPH’s production sites amounted to 16 554 tonnes, which compares to 18 124 tonnes the previous year. Of these, 9 672 tonnes derived from paper production. The sales of carbon credits generated an income of CHF 1.0 million.
Exhaust air cleaning systems are installed at the Group’s production facilities. Emergency concepts have been devised to cope with any production malfunction. These centre largely on the scenario of fire. The Perlen site has its own fire service which can be deployed if needed. The handling of acids and sodium hydroxide at the Uetikon plant posed a potential environmental threat. The CPH Group again completed the year free of any incident subject to reporting requirements. The waste water produced by the Group’s Uetikon, Perlen and Louisville plants was processed in their own treatment facilities. Paper manufacturing also produces solid waste, largely in the form of sludge and residual waste. The biomass here is used to produce heat and electricity in the Group’s own Perlen facility.
Brand policy
The CPH Group pursues an individual brand policy. CPH Chemie + Papier Holding AG, the Group’s holding company, is not operationally active, but serves as an umbrella brand towards stakeholders, particularly investors and the public. The Group’s three divisions are well established in their target markets as “Zeochem”, “Perlen Papier” and “Perlen Packaging”. To ensure consistent brand identities, all the subsidiaries in the Chemistry and Packaging Divisions are to be renamed Zeochem and Perlen Packaging respectively.
Quality
Consistently high quality is a hallmark of all CPH products. This makes stringent demands on processes, which are audited to international standards (see table below). The Packaging Division aligns its film manufacturing to the pharmaceuticals sector’s Good Manufacturing Practice, and was recertificated to Norm 2015 for ISO 9001 and ISO 15378 in 2017. The CPH Group also promotes energy efficiency in the climate protection project of the Swiss private sector’s energy agency, and is a member of Responsible Care, a global continuous improvement initiative in the environmental, health and safety fields.